Predictive Maintenance Using AI in the Automotive Industry
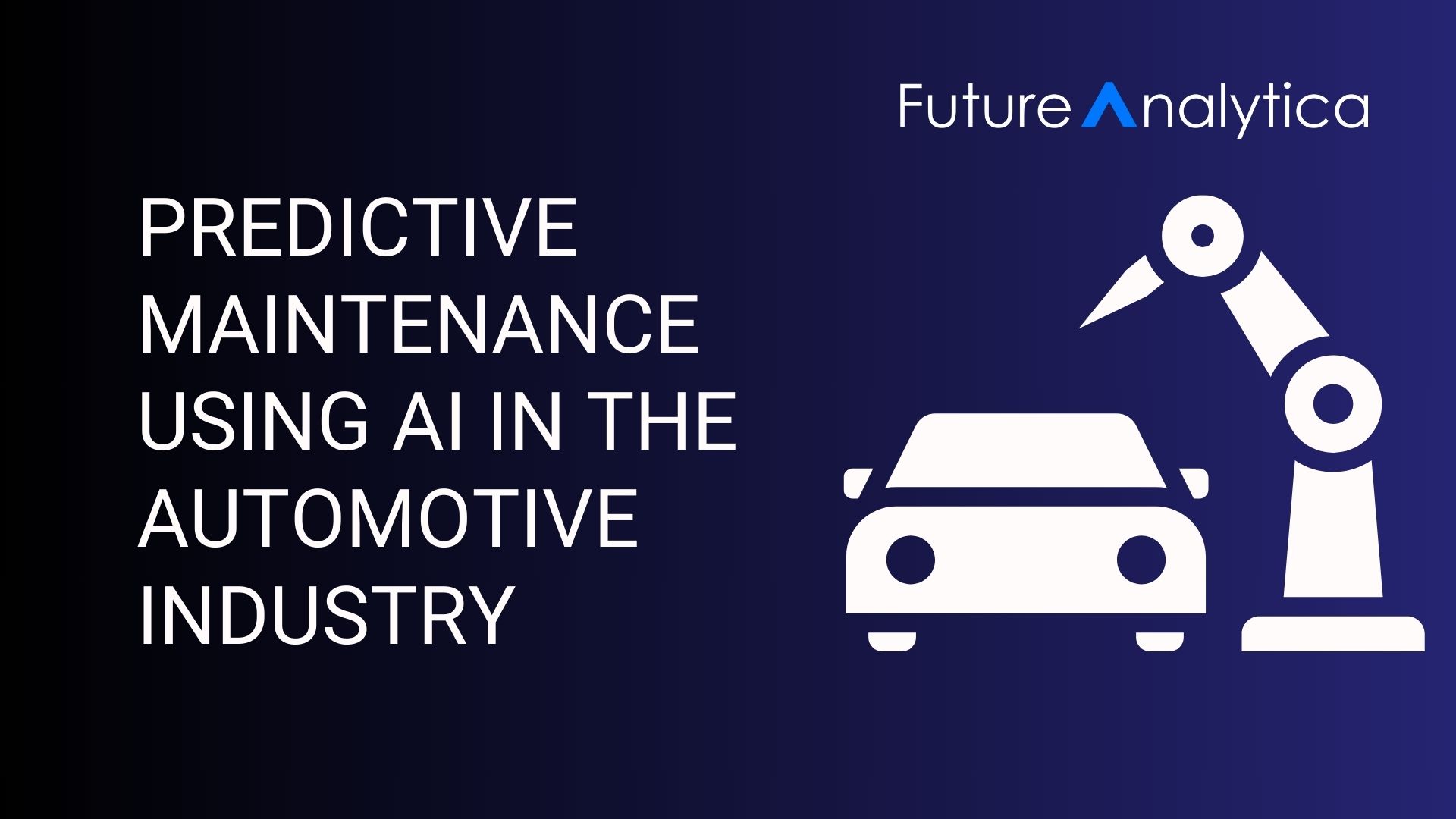
In the rapidly evolving automotive industry, the integration of Artificial Intelligence (AI) into predictive maintenance strategies is transforming how manufacturers and fleet managers approach vehicle service and repairs. Predictive maintenance, powered by AI, not only enhances vehicle safety and efficiency but also significantly reduces downtime and maintenance costs. At FutureAnalytica, we are at the forefront of leveraging these advanced technologies to offer cutting-edge solutions that align with the needs of modern automotive enterprises.
How Predictive Maintenance Works in the Automotive Industry
Data Collection and Analysis
Predictive maintenance starts with the continuous collection of data from various sensors installed in a vehicle. These sensors monitor critical parameters such as engine temperature, vibration levels, brake wear, and more. The data collected is vast and detailed, providing a comprehensive view of the vehicle’s operational status at any given time
Utilization of Machine Learning and AI
The collected data is then analyzed using machine learning algorithms and AI. These technologies are capable of identifying patterns and anomalies in the data that may indicate potential issues or upcoming failures. For instance, if the data shows an unusual increase in engine temperature or abnormal vibrations, it could suggest problems like a failing engine component or issues with the vehicle’s alignment
Predictive Analytics
After analyzing the data, predictive models are developed. These models use historical data along with real-time information to predict potential failures. For example, by understanding the typical performance data and the current operational data, the system can forecast when a specific component like a brake pad or battery might fail
Maintenance Alerts
Once a potential issue is identified, the system generates alerts for the vehicle owner or maintenance team. This proactive approach allows for scheduling maintenance or repairs before the component fails, ensuring the vehicle remains operational without unexpected breakdowns. This not only saves on costly emergency repairs but also significantly reduces vehicle downtime
Benefits of AI-Driven Predictive Maintenance
AI-driven predictive maintenance is transforming the automotive industry by enhancing efficiency, safety, and reliability while significantly reducing operational costs. Here are five key benefits of integrating AI-driven predictive maintenance into the automotive sector:
- Reduced Operational Costs: One of the most significant benefits of AI-driven predictive maintenance is the substantial reduction in operational costs. By predicting equipment failures before they occur, automotive companies can avoid costly downtime and emergency repairs. This proactive approach to maintenance allows for better planning and scheduling of maintenance activities, leading to more efficient use of resources and reduced labor costs. Predictive maintenance helps in identifying the exact maintenance needs, eliminating unnecessary checks and replacements, thus saving on spare parts and reducing waste
- Enhanced Maintenance of Manufacturing Equipment: AI-driven predictive maintenance significantly improves the maintenance of automotive manufacturing equipment. By continuously monitoring the condition of machinery and analyzing data for signs of wear or impending failure, predictive maintenance systems can alert maintenance teams to specific issues that need attention. This targeted approach prevents minor issues from escalating into major failures that could halt production, ensuring that manufacturing equipment operates at optimal efficiency and extends the lifespan of costly machinery
- Optimized Use of Equipment Sensors: The integration of AI with equipment sensors represents a leap forward in maintenance strategies. Sensors collect real-time data on various parameters such as temperature, vibration, and pressure, which AI algorithms analyze to detect anomalies and predict potential failures. This data-driven approach allows for a more nuanced understanding of equipment health and performance, enabling automotive companies to pinpoint maintenance needs with unprecedented accuracy. The optimization of sensor data through AI not only enhances predictive maintenance efforts but also contributes to the overall intelligence and automation of the manufacturing facility
- Improved Manufacturing Facility Efficiency: AI-driven predictive maintenance contributes to the overall efficiency of automotive manufacturing facilities. By minimizing unplanned downtime and ensuring that equipment operates reliably, predictive maintenance supports continuous, uninterrupted production. This reliability is crucial for meeting production targets and maintaining the supply chain’s integrity. Furthermore, the insights gained from predictive maintenance can inform operational improvements and optimizations, leading to increased productivity and reduced manufacturing costs
- Increased Equipment and Facility Safety: Safety in the manufacturing facility is significantly enhanced through AI-driven predictive maintenance. By identifying potential equipment failures before they occur, predictive maintenance can prevent accidents that might result from equipment malfunction. This proactive approach to maintenance not only protects the workforce but also minimizes the risk of damage to the manufacturing facility and the environment. Ensuring equipment operates within safe parameters contributes to a safer, more compliant manufacturing environment
What are some challenges in implementing predictive maintenance in the automotive industry?
Implementing predictive maintenance in the automotive industry presents several challenges, which can impact the effectiveness and efficiency of these systems. Here are some of the key challenges:
- Data Collection and Management: Gathering large amounts of high-quality data is essential for effective predictive maintenance. However, collecting this data can be challenging due to the need for extensive sensor networks and the complexity of vehicle systems. Managing and storing this vast amount of data also poses significant challenges
- High Initial Costs: The initial setup for predictive maintenance systems, including the installation of sensors and the development of the necessary infrastructure for data analysis, can be costly. These upfront costs can be a significant barrier, especially for smaller automotive companies or those with limited budgets
- Complexity of Implementation: Transitioning from traditional maintenance methods to a predictive maintenance system involves a complex overhaul of existing processes. This includes integrating new technologies and training staff to operate and maintain these systems effectively
- Accuracy and Reliability of Predictions: Ensuring the accuracy and reliability of the predictive models is crucial. Inaccurate predictions can lead to unnecessary maintenance actions or missed maintenance opportunities, which can be costly and reduce trust in the system
- Security Concerns: With the increased use of IoT devices and the collection of large amounts of data, security becomes a critical concern. Protecting sensitive data against cyber threats is essential to maintain the integrity and confidentiality of the predictive maintenance systems
- Skilled Personnel: The successful implementation of predictive maintenance requires a team of skilled personnel who are trained in both the technology and its application within the automotive industry. There is often a shortage of such skilled personnel, which can hinder the deployment and ongoing management of predictive maintenance systems
- Integration with Existing Systems: Integrating predictive maintenance technologies with existing automotive systems and processes can be challenging. Compatibility issues may arise, requiring additional resources and adjustments to ensure seamless integration
These challenges highlight the need for careful planning, significant investment, and ongoing management to successfully implement and maintain predictive maintenance systems in the automotive industry.
Real-World Applications and Success Stories
Several leading automotive manufacturers and fleet operators have successfully integrated AI-driven predictive maintenance systems. For instance, a major automotive manufacturer implemented an AI system that predicts battery life span and other critical components’ failures. This system has not only reduced the downtime but also enhanced the efficiency of the fleet by ensuring timely maintenance.
Another example is a logistics company that uses AI to monitor engine performance and tire wear. The predictive maintenance system has helped them reduce tire replacement costs by 20% and increase vehicle availability by 15%.
Future Directions
The future of predictive maintenance in the automotive industry looks promising with continuous advancements in AI and machine learning technologies. The integration of Internet of Things (IoT) devices and more sophisticated sensors is expected to further improve the accuracy and efficiency of predictive maintenance systems. Additionally, as electric vehicles become more prevalent, predictive maintenance will play a crucial role in monitoring and maintaining battery health and other specific components critical to electric vehicle operations.
Conclusion
At FutureAnalytica, we understand the critical role of predictive maintenance in the automotive industry. Our solutions are designed to harness the power of AI to provide real-time insights and predictive analytics, ensuring that your automotive operations are efficient, safe, and cost-effective. As the industry continues to evolve, we remain committed to innovating and delivering solutions that meet the needs of modern transportation and logistics.
For more information on how AI-driven predictive maintenance can transform your automotive operations, visit our website at www.futureanalytica.com. Join us in driving the future of automotive maintenance with advanced AI solutions.